8 Types Of Waste In Lean Construction
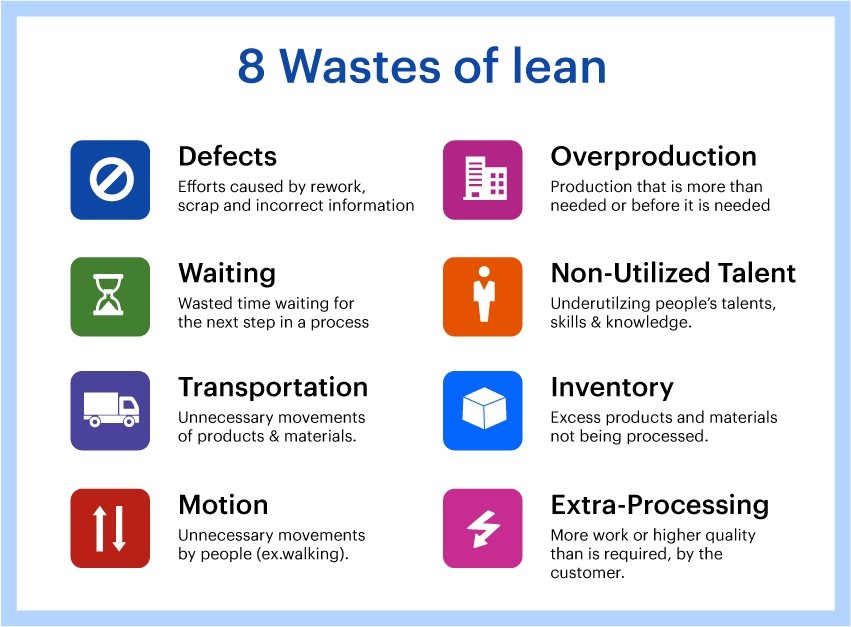
8 Wastes Of Lean How To Identify And Eliminate Them The lean construction institute is committed to transforming the design and construction industry by providing lean educational resources, conducting field research, and facilitating local and national lean events. explore supplementary resources below to further your understanding of the 8 wastes and how to mitigate them. 8) skills and underutilized talent. the 8th waste of lean involves failing to make use of people’s skills, creativity, or knowledge on a project. this is not one of the traditional seven wastes (or seven mudas) found in early lean literature, but is now commonly accepted as an additional waste of lean, and turns the common mnemonic for the 7.
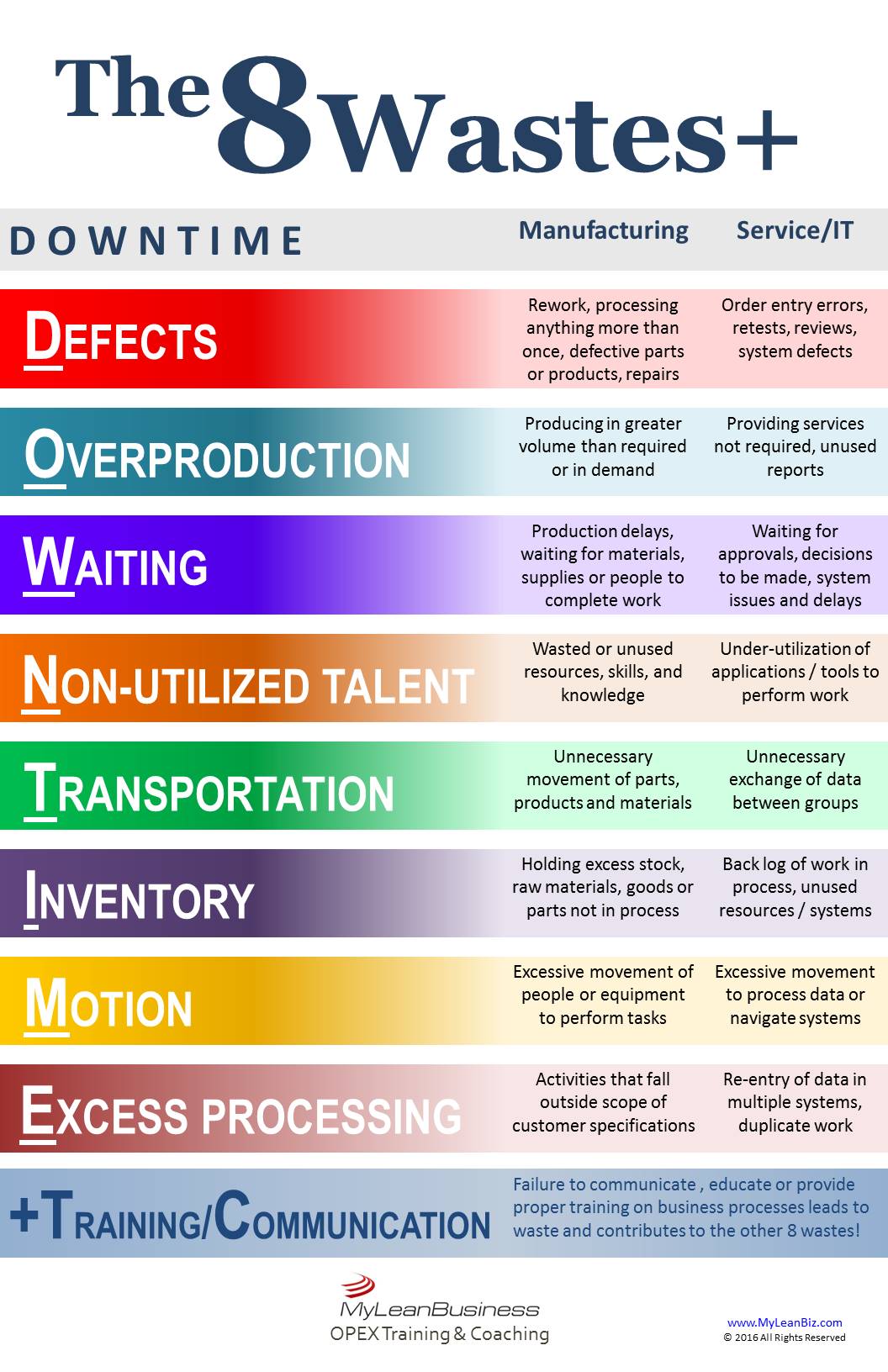
The 8 Wastes Lean Poster Myleanbusiness Inc 8. skills the 8th waste. even though it was not part of the toyota production system (tps), many people are well aware of the 8th waste the waste of human potential. the 8th waste is also described as the waste of unused human talent and ingenuity. this waste occurs when organizations separate the role of management from employees. Lean construction is a methodology inspired by lean manufacturing principles. it seeks to identify and eliminate waste to enhance value and streamline operations. before you can eliminate waste, you have to identify it. the eight wastes of lean construction are: defects, overproduction, waiting, non utilized talent, transportation, inventory. Read 6 min introduction in lean construction, identifying and eliminating waste is crucial for achieving operational excellence. here, we’ll explore the eight types of waste, how they impact construction projects, and provide actionable tips for reducing or eliminating them. the eight types of waste overproduction: creating more of a product than needed. this leads to excess inventory and […]. Absolutely. waste exists in all organizations, and the 8 wastes can be identified and eliminated in any type of organization. on a final note: the 8 wastes of lean the 8 wastes of lean exist in every organization and are all around you. you walk by it everyday and can become desensitized to its existence. waste can create a frustrating and.

8 Wastes Of Lean Manufacturing Techsolve Read 6 min introduction in lean construction, identifying and eliminating waste is crucial for achieving operational excellence. here, we’ll explore the eight types of waste, how they impact construction projects, and provide actionable tips for reducing or eliminating them. the eight types of waste overproduction: creating more of a product than needed. this leads to excess inventory and […]. Absolutely. waste exists in all organizations, and the 8 wastes can be identified and eliminated in any type of organization. on a final note: the 8 wastes of lean the 8 wastes of lean exist in every organization and are all around you. you walk by it everyday and can become desensitized to its existence. waste can create a frustrating and. The eight wastes of lean. originally there were seven wastes identified by taiichi ohno for the toyota production system. as lean evolved into the rest of the enterprise and around the world, an eighth waste, non utilized talent, was identified. jean cunningham and others use an acronym, “downtime”, to help remember the wastes. Inadequately stocked examination rooms. unorganized workspaces, processes without standardization, and inadequate understanding of customer behavior can all lead to the waste of motion. 5. overproduction. nowadays, just about everyone is familiar with just in time manufacturing and inventory management.

Lean 8 Wastes Chart The eight wastes of lean. originally there were seven wastes identified by taiichi ohno for the toyota production system. as lean evolved into the rest of the enterprise and around the world, an eighth waste, non utilized talent, was identified. jean cunningham and others use an acronym, “downtime”, to help remember the wastes. Inadequately stocked examination rooms. unorganized workspaces, processes without standardization, and inadequate understanding of customer behavior can all lead to the waste of motion. 5. overproduction. nowadays, just about everyone is familiar with just in time manufacturing and inventory management.
Comments are closed.