8 Wastes Of Lean How To Identify And Eliminate Them
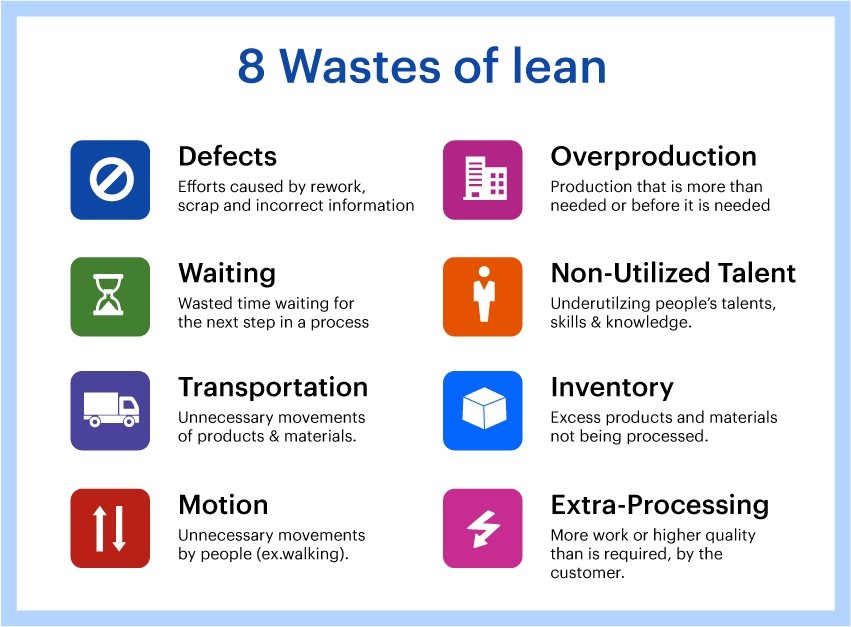
8 Wastes Of Lean How To Identify And Eliminate Them Therefore, the acronym was expanded to “timwoods”. alternatively, i prefer to use the acronym “downtime” to refer to the 8 wastes of lean. in this case, the 8 wastes are ordered as follows: defects. overproduction. waiting. non utilized talent. transportation. Waiting. overproduction. overprocessing. defects. these seven wastes were referred to as timwood, but the eighth waste was added to the list. skills, the eighth waste, was later introduced making the acronym timwoods. the article below has a brief description of each waste and how to minimize them using lean six sigma.
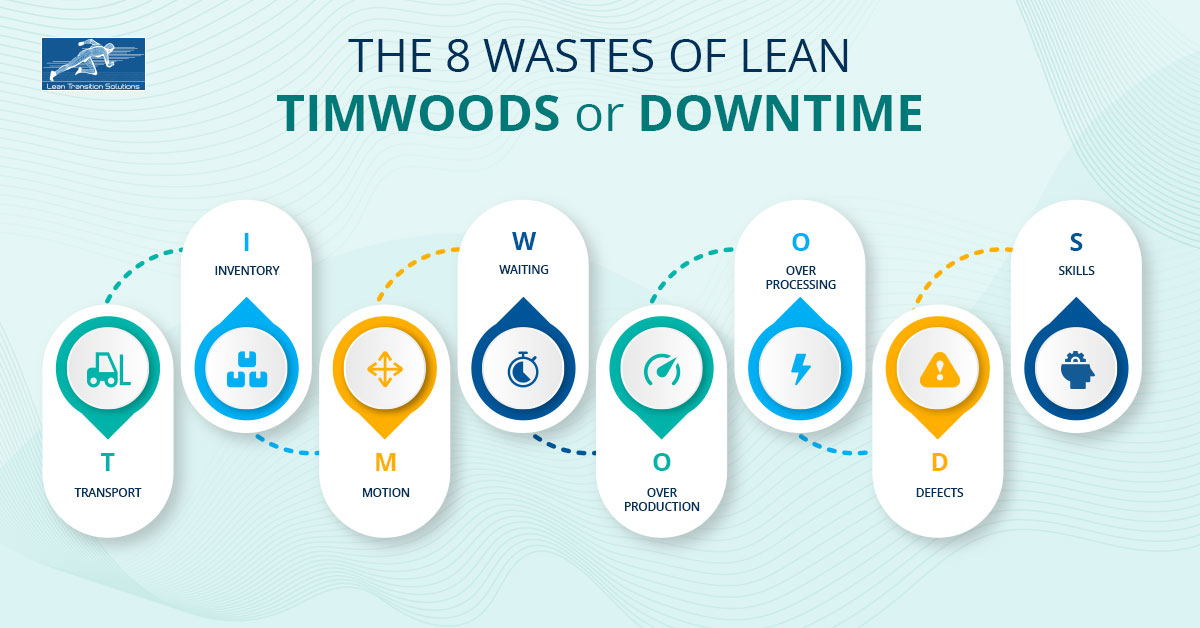
8 Wastes Of Lean How To Identify And Eliminate Them Vrogue Co Identifying and eliminating the 8 wastes. the first step to reducing waste is recognizing that they exist and having an effective process for identifying them. in order to identify wastes, start with the end customer in mind. work backwards from the end customer to the start of the production processes. Overproduction. waiting. non utilized talent. transportation. inventory. motion. extra processing. identifying and addressing these wastes is fundamental to lean principles and contributes to streamlined and efficient processes. here’s a more detailed explanation of each of the 8 wastes. Step 1: assessment. conduct a thorough assessment to identify the eight wastes in your organization, evaluating their impact on efficiency, cost, and goals. step 2: prioritization. prioritize identified wastes based on severity and influence for a focused and strategic approach. step 3: strategic planning. 8 lean wastes: how to identify & eliminate them. one of the first steps in applying lean concepts on a path to operational excellence is identifying and eliminating waste. in the old days of manufacturing, this might have been called scrap. the japanese tps system, upon which lean is modelled, focuses on delivering value to the customer.
Comments are closed.