Key Tips For Making Molds With 3d Printing

3d Printed Molds Casting Tutorial Complex Shapes 12 Steps 58 Off To create a 3d printed mold, you first need to choose a suitable material. the result when printing it on an fdm printer with abs or pla will most likely lack the detail needed and require too much cleanup to make printing the mold feasible. every flaw in the 3d printed mold will be reproduced in the cast, so we need to create the mold with a. 3d printed molds tutorial: how to diy your own. by ross lawless. updated jul 14, 2023. using your 3d printer to create molds is not only possible but easy. check out our simple guide on how to make 3d printed molds yourself!.

Create Molds With Keys For 3d Printing Convert Blender Models Into 3d Cast molding is a type of manufacturing that uses a liquid material to create molds for casting. the cast molding process begins by heating a raw material until it becomes liquid. the liquid is then poured into a mold created by 3d printing or another method. as the material cools and hardens it takes the shape of the mold. You can use a regular microwave with maximum settings, for about one minute (depends on the microwave output and which exact soap material you use). to be on the safe side, we recommend checking the situation every 30 seconds. tape both mold halves tightly together. pour the hot material slowly into the mold. Step 2: mold box and parting line. arrange your original object square to how you decided the mold should be printed. draw a 3d box around your original, leaving at least a centimeter or so around all sides. you can cut it down later to save on material (a good idea if you are using a service that charges by volume). Stern design works uses an ultimaker 3 to create jigs and molds for jewelry. “with 3d printing, you can make one piece or 10 iterations of something, and you have 10 tries to get a perfect piece back from the foundry,” rebecca stern, cofounder of stern design works, said. “and working with a 3d printed piece versus a wax piece takes a.

Mold Design With Sla 3d Printing Forge Labs Step 2: mold box and parting line. arrange your original object square to how you decided the mold should be printed. draw a 3d box around your original, leaving at least a centimeter or so around all sides. you can cut it down later to save on material (a good idea if you are using a service that charges by volume). Stern design works uses an ultimaker 3 to create jigs and molds for jewelry. “with 3d printing, you can make one piece or 10 iterations of something, and you have 10 tries to get a perfect piece back from the foundry,” rebecca stern, cofounder of stern design works, said. “and working with a 3d printed piece versus a wax piece takes a. 8. pour silicone into the 3d printed mold. once the mold is printed (and you’ve taken a few moments to admire your handiwork), it’s time to form the actual cast inside your 3d printed mold. mix the silicone according to the instructions on the pack, and pour it into the mold. Engraving and embossing – make sure these features are pronounced enough in the molded part. some resources suggest a minimum offset of 1 mm should be used. post processing – remember that 3d.
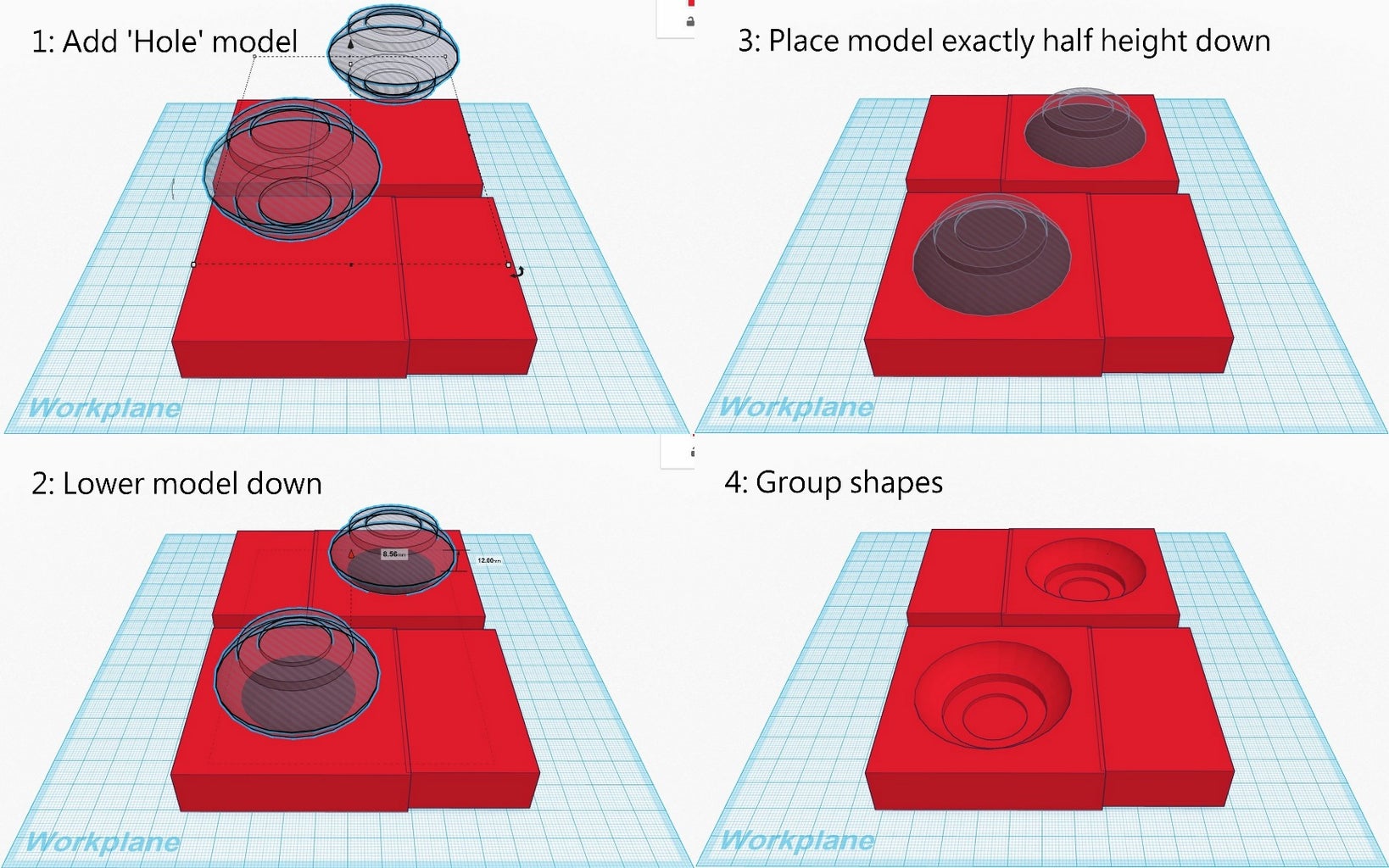
3d Printed Molds Casting Tutorial Complex Shapes 12 Steps With 8. pour silicone into the 3d printed mold. once the mold is printed (and you’ve taken a few moments to admire your handiwork), it’s time to form the actual cast inside your 3d printed mold. mix the silicone according to the instructions on the pack, and pour it into the mold. Engraving and embossing – make sure these features are pronounced enough in the molded part. some resources suggest a minimum offset of 1 mm should be used. post processing – remember that 3d.
Comments are closed.