Mold Making And Die Casting At Shirley Collins Blog

Mold Making And Die Casting At Shirley Collins Blog The unit die is a special type of die casting mould. a die caster unit holder keeps the unit dies or customer owned cavity within the cavity intact. we can have either single or double unitholders. typical examples of sizes of cavity blocks that the dies hold are 8 x 10, 10 x 12, 12 x 15, and 15 x 18 (all in inches). To be on the safe side, we recommend checking the situation every 30 seconds. tape both mold halves tightly together. pour the hot material slowly into the mold. it will solidify in about 1 3 hours, depending on the ambient temperature (you could put it into a fridge to speed things up).
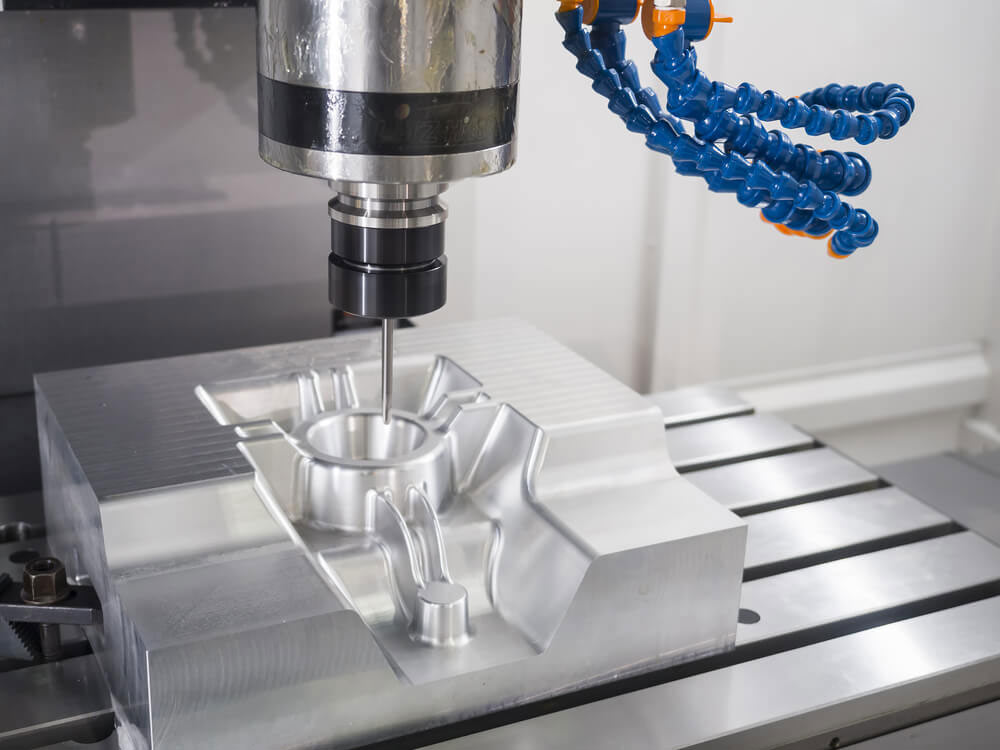
Mold Making And Die Casting At Shirley Collins Blog Table of contents. step 1: design and specification. step 2: tooling and mold base preparation. step 3: mold assembly and finishing. step 4: testing and validation. step 5: production and maintenance. conclusion. start a die casting project with the federal group today. The mold design should fit the economy and feasibility. (1) the overall structure of the mould is simple and practical, and the comprehensive cost is low. (2) economical and practical dimension matching accuracy should be selected. (3) reduce the consumption of surplus materials in the pouring system. 5. Processes, materials, applications, costs. published: april 30, 2024 reading time: about 3 minutes. die casting transforms a vision into reality, enabling the precise creation of intricate metal components that are the backbone of today’s leading industries—from automotive to electronics. at its core, this process involves the high pressure. After the mold has been assembled, the casting process begins. once it’s completed, the mold needs to be carefully opened and the excess sand gently shaken off. doing so ensures that the cope can be pulled away from the casting with relative ease. in most cases, the cope is broken off, allowing for easy removal.
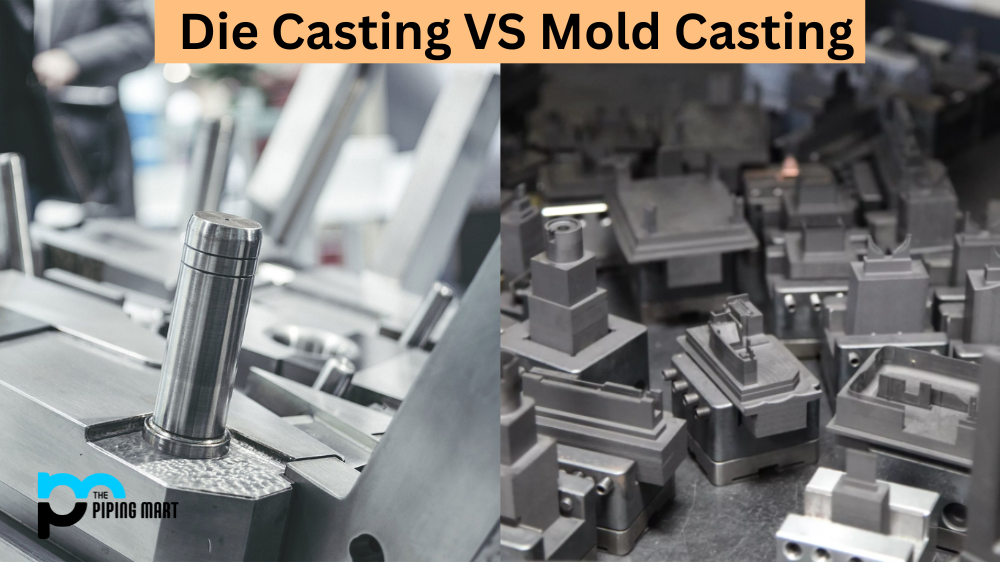
Mold Making And Die Casting At Shirley Collins Blog Processes, materials, applications, costs. published: april 30, 2024 reading time: about 3 minutes. die casting transforms a vision into reality, enabling the precise creation of intricate metal components that are the backbone of today’s leading industries—from automotive to electronics. at its core, this process involves the high pressure. After the mold has been assembled, the casting process begins. once it’s completed, the mold needs to be carefully opened and the excess sand gently shaken off. doing so ensures that the cope can be pulled away from the casting with relative ease. in most cases, the cope is broken off, allowing for easy removal. Die casting is a process that uses high pressure to force molten metal into a mould. mold casting is a process that uses gravity to fill a mould with molten metal. die casting produces parts that are more precise and have a better surface finish than those produced by mould casting. die casting is typically more expensive than mould casting. Zinc die casting is a process involving the injection of liquid zinc metal under pressure into a mold and left to solidify. the mold cavity is made from two hardened tool steel molds designed to your desired shape. zinc alloys have low melting points, hence the casting proceeds under lower heat.
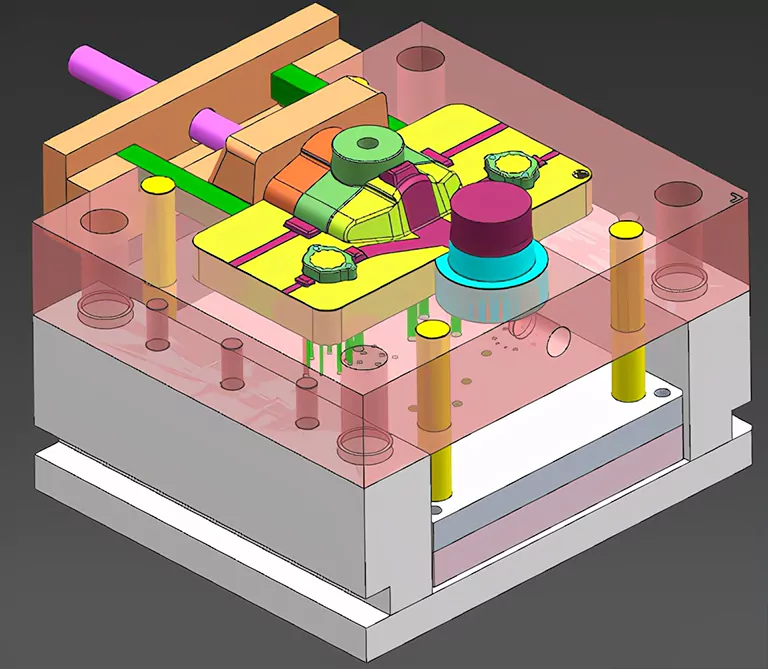
Die Casting Mold Designing Tips 7 Steps Guide From Expert Die casting is a process that uses high pressure to force molten metal into a mould. mold casting is a process that uses gravity to fill a mould with molten metal. die casting produces parts that are more precise and have a better surface finish than those produced by mould casting. die casting is typically more expensive than mould casting. Zinc die casting is a process involving the injection of liquid zinc metal under pressure into a mold and left to solidify. the mold cavity is made from two hardened tool steel molds designed to your desired shape. zinc alloys have low melting points, hence the casting proceeds under lower heat.
Comments are closed.