Types Of Bends

Bend Types A 1 Roll Company Learn about the four types of pipe and pipeline bends: hot bends, cold bends, elastic bends, and miter bends. find out how they are manufactured, used, and regulated in the oil and gas industries. However, the shortest edge of the z bend is larger than that of the l bend, owing to the structure of the lower die. the formula used to calculate the minimum edge of the z bend is: l min =1 2(b min Δ) d 0.5 t ③. l min refers to the shortest bend edge, while bmin is the minimum mold width. Δ represents the bending coefficient of the.
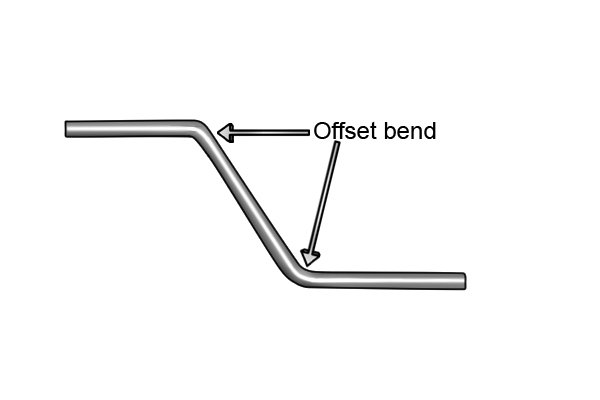
What Are The Types Of Bend Miter bends. another type of bend is a miter bend. a miter bend is a bend that is made by cutting pipe ends at an angle and joining the pipe ends. a true miter bend is a 90 degree bend made by cutting two pipes at 45 degrees and joining them by welding. similarly, three pipes cut at 22.5 degrees will give a 90 degree miter bend. Specialty tube bending processes abound, some old and some new. most tubes, though, are bent one of four ways: ram type bending, roll bending, compression bending, or rotary draw bendin g. figure 1. pipe is specified by its nominal pipe size, while tube is specified by its outside diameter. 2. bends where the flanges aren’t adjoining. flange in sheet metal parts, is a feature that consists of a face and bend connected to an existing face along a straight edge. for bends where the flanges aren’t adjoining, there are a number of different relief types available for utilisation by designers. two of the most common types include:. There are generally four (4) different methods of tube pipe bending that can also be classified according to complexity. you’ll encounter the following: compression bending, rotary draw bending, roll bending, and mandrel tube bending. each of these processes achieves a precision bending in order to make the pipe suitable for application.

Typical Bending Types Applied To Progressive Die Design Download 2. bends where the flanges aren’t adjoining. flange in sheet metal parts, is a feature that consists of a face and bend connected to an existing face along a straight edge. for bends where the flanges aren’t adjoining, there are a number of different relief types available for utilisation by designers. two of the most common types include:. There are generally four (4) different methods of tube pipe bending that can also be classified according to complexity. you’ll encounter the following: compression bending, rotary draw bending, roll bending, and mandrel tube bending. each of these processes achieves a precision bending in order to make the pipe suitable for application. K – k factor, constant; ir – inside radius (mm); t – sheet thickness (mm) bend allowance formulas: for bends between 0 and 90 degrees, the formula is as follows: ß – bending angle (°) for bends between 90 and 165 degrees the formula is: for bends over 165°, there is no need to calculate bend allowances, as the neutral axis stays. Jog bends. both jog bends and material offset bends are often used for adding clearance to a design. while jog bends and material offset bends achieve a similar result, the bending process for each is different. material offset bends are performed in a single operation, while jog bends are performed in two separate operations. learn more.
Comments are closed.