Waste Of Waiting Causes Symptoms Examples And Solutions
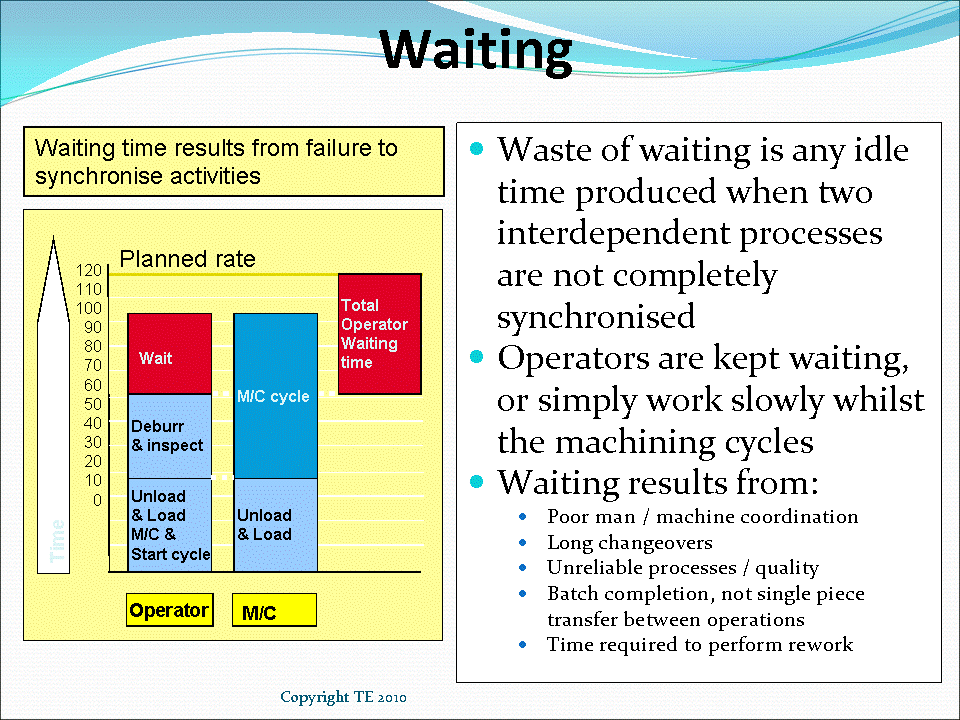
Waste Of Waiting Causes Symptoms Examples And Solutions Examples of wastes of waiting. operators machines standing idle whilst they wait for a previous processes production to be sorted due to quality problems. waiting for a breakdown to be resolved. waiting for a previous process to complete a batch of material prior to movement. waiting for the forklift truck to deliver a batch of components. Examples of wastes of motion. a machine that travels excessive distance from start point to where it begins work. heavy objects placed on low or high shelves. searching for tools and equipment. walking across work space to retrieve components or use machines.

Waste Of Waiting Causes Symptoms Examples And Solutions 55 Off The waste of resources; failing to conserve your electricity, gas, water and any other resources you rely on. the waste of creativity; failure to respect and involve your employees in your business. transportation is one of the seven wastes of lean manufacturing (7 muda), this post will give causes, symptoms, examples, costs and solutions. Whatever the case, this waste, like all other waste, must be identified and eliminated. parts shortages causing waiting. when a line or production area encounters a part shortage, it is very easy to see that people are standing around waiting for the parts to arrive. this type of event will usually draw much attention and get highlighted quickly. We define all wastes that occur in production, logistics or service processes as time waste. we can categorize waiting lean wastes into three basic categories: the first category of waiting – when a person waits for a machine. the second category is when a person waits for another person. the third category – when a person waits for material. Waiting in one meeting may not be so bad, but knowledge workers may spend a third or even half of their time in meetings, and this number can be more for the highest paid executives. in knowledge work, waiting caused by delays can create a chain reaction of waste. there are multiple cause for waiting, so multiple countermeasures are required.

Forms Of Waste Waiting We define all wastes that occur in production, logistics or service processes as time waste. we can categorize waiting lean wastes into three basic categories: the first category of waiting – when a person waits for a machine. the second category is when a person waits for another person. the third category – when a person waits for material. Waiting in one meeting may not be so bad, but knowledge workers may spend a third or even half of their time in meetings, and this number can be more for the highest paid executives. in knowledge work, waiting caused by delays can create a chain reaction of waste. there are multiple cause for waiting, so multiple countermeasures are required. An eighth waste was added in the 1990s as the toyota production system was adopted by manufacturers in the rest of the world as lean manufacturing. the eight wastes are represented by a mnemonic, timwoods, which stands for transportation, inventory, motion, waiting, overproduction, over processing, defects, and unused skills. Facilities often overproduce things like paperwork, reports, meetings, and packaging, all of which waste resources. 2. waiting. unanticipated delays are ubiquitous in manufacturing operations. for many, time spent waiting is the second most costly form of waste. rhythm is essential in manufacturing to ensure tools, materials, labor, and.

Waste Of Waiting Causes Symptoms Examples And Solutions 55 Off An eighth waste was added in the 1990s as the toyota production system was adopted by manufacturers in the rest of the world as lean manufacturing. the eight wastes are represented by a mnemonic, timwoods, which stands for transportation, inventory, motion, waiting, overproduction, over processing, defects, and unused skills. Facilities often overproduce things like paperwork, reports, meetings, and packaging, all of which waste resources. 2. waiting. unanticipated delays are ubiquitous in manufacturing operations. for many, time spent waiting is the second most costly form of waste. rhythm is essential in manufacturing to ensure tools, materials, labor, and.
Comments are closed.